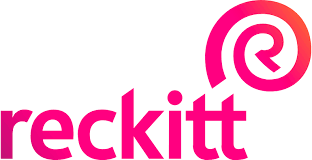
Reliability Engineer
Reckitt Benckiser
- Wanamingo, MN
- Permanent
- Full-time
- Responsible for resolving issues in technical operations, training, and maintenance of machines and equipment. Daily monitoring of OEE to include identifying, documenting, and prioritizing, to address issues which impact site performance.
- Collect performance data on equipment and components. Analyze, tabulate, and present the data collected to justify equipment component or asset repair or replacement.
- Utilize downtime data and repair cost to determine the ROI (payback) of repair or replacement. Provide trade-off data analysis to justify the recommendations.
- Advise and assist in the selection of suppliers and vendors to ensure equipment meets Reckitt Standards for safety, food safety, and operational performance.
- Manage the activities of the Predictive Maintenance Technician. Analyze maintenance and downtime records to determine repetitive issue.
- Advise of necessary level of spare parts in maintenance tool room to ensure adequate quantities are held on site. This analysis will follow the Reckitt SOP for tool room prioritization of parts and quantity decision tree to mitigate downtime risks.
- Assist in identifying critical spare parts for new and existing equipment.
- Keep the technical documentation of all plant operational equipment up to date and readily available for the mechanics and the L&D (Learning and Development) teams.
- Participation in Factory Acceptance (FATs) and Site Acceptance Tests (Line Commissioning) and coordinate with project managers to resolve open equipment and process issues.
- Coordinate training of technical and operational personnel in conjunction with L&D. Training includes all aspects of machine operation, critical and routine maintenance.
- Participate in Maintenance budgeting to gain understanding of high costs to maintain.
- Communicate with vendors and suppliers to gain understanding of long lead time parts and services and know which parts/components are moving into obsolescence. Coordinate projects with the project management and engineers to replace obsolete components and equipment.
- Technical skills-technical knowledge of components, technologies, and principles of operation used in packaging, processing, and facility equipment used in the Wanamingo Facility
- Analytical Skills -Must have the ability to collect and analyze information, problem-solve, and make independent decisions based on data. (FMEA, RCA, Fault Tree, Reliability Block-diagram)
- Organizational Skills - Work with internal (Project Engineers, Maintenance Technicians, Operators) and external stakeholders (Service technicians, Vendors, Suppliers) to plan activities leading to achieving organizational goals.
- Technology Proficiency - Computer Literacy Skills - MS Office, SAP
- Preferred hands-on knowledge of SAP, AutoCAD, and Allen Bradley PLC/Screen Software
- Must be able to frequently stand, stoop, bend, reach overhead, walk, climb/ work from heights, and lift up to 50 pounds
- College degree: Bachelor of Science in Industrial, Chemical, Mechanical, or Electrical Engineering
- Equivalent combination of education and experience may be considered in lieu of a Bachelor's degree.
- Experience: 5 + years working with high-speed automated packaging and filling equipment in CPG or Food Manufacturing.
- Experience with MES is desirable